Fittings instead of waste
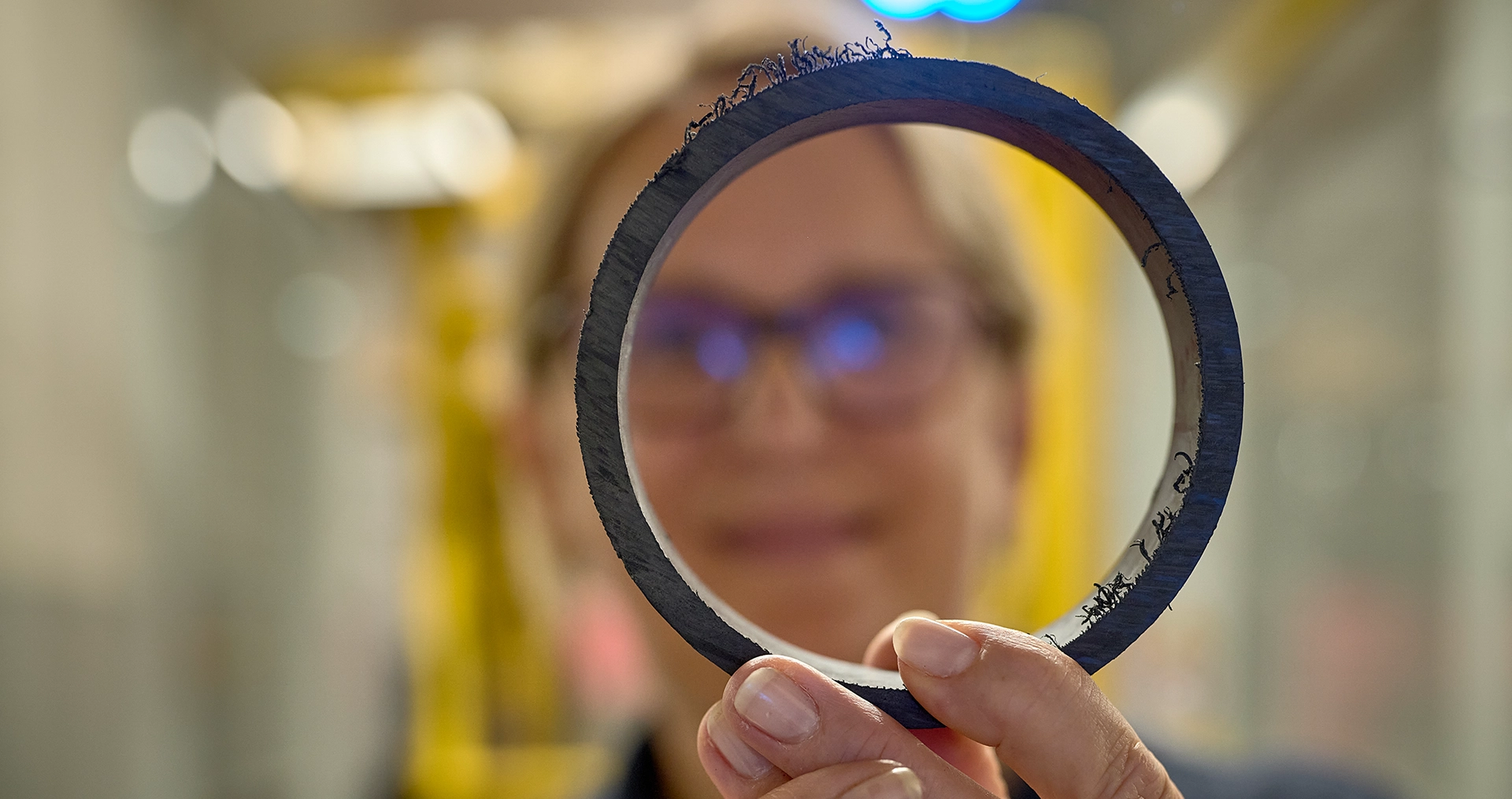
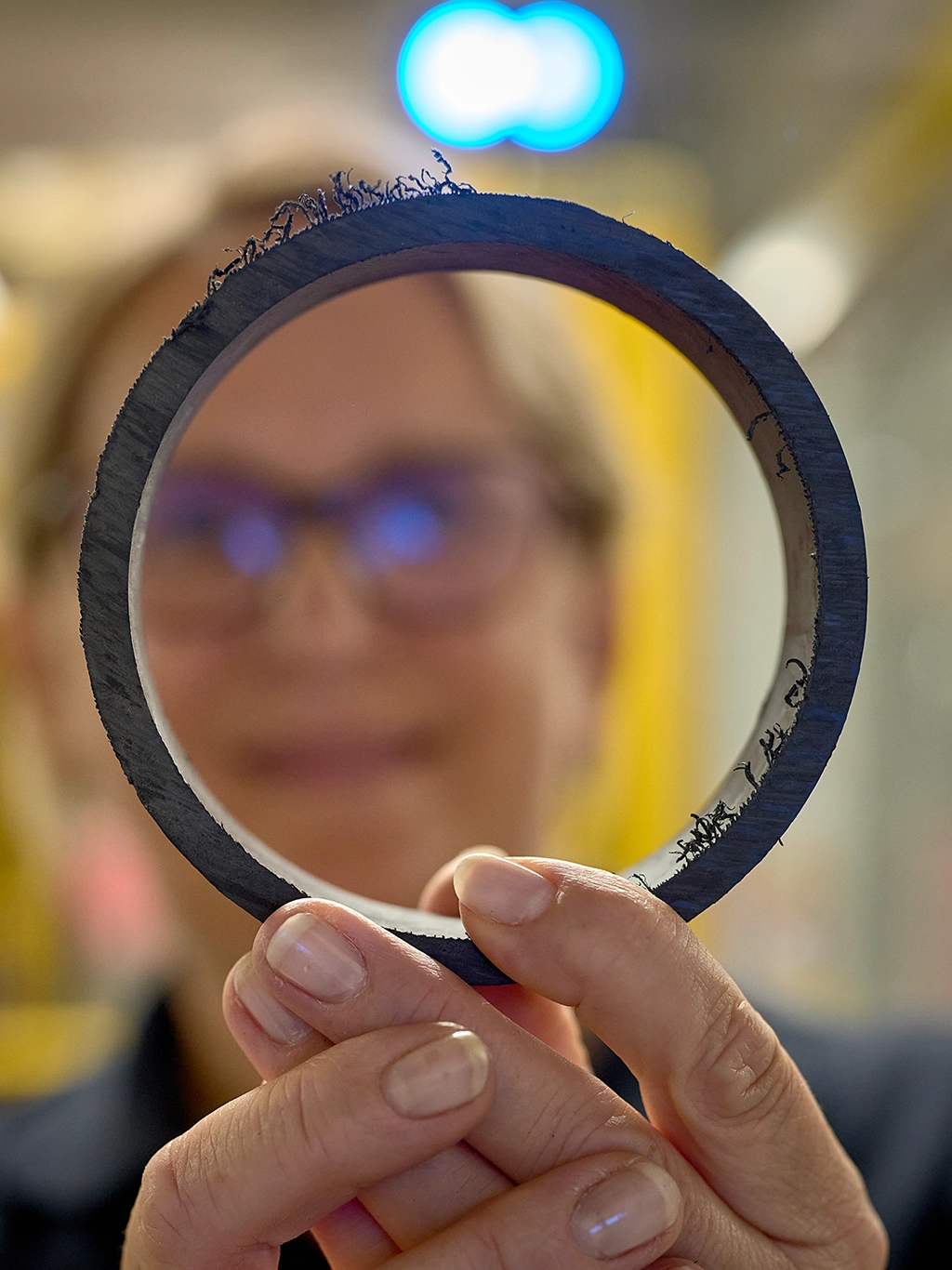
In Rapperswil-Jona (CH), Geberit produces new fittings from unused pipe cut-offs. This innovative pilot project not only saves raw materials, but is also environmentally beneficial.
Leftovers are a common sight at the breakfast table, especially the end slice of the bread loaf is often left uneaten. Instead of throwing these away, home cooks transform them into croutons or breadcrumbs. These “cut-offs” then don’t end up on the compost heap or in the waste bin.
A pilot project at Geberit in Rapperswil-Jona (CH) takes the same approach. Instead of bread scraps, leftover plastic pipes are being reused here. At the production plant, cut-offs of Silent-db20 pipe pieces are ground up and used for the production of new fittings.
Processing scraps is cheaper than buying new material.
20%
reused material
A new fitting can contain up to one-fifth reused material.
Scraps from the prefabrication industry
The leftover pipes – commonly known as scraps – come from PE Fabrikations AG, a prefabricator in the Swiss sanitary trade. Here, employees weld together dozens of discharge pipes every day on behalf of sanitary companies. The prefabricated pipes reduce the installation time on the construction site significantly. Waste is produced as a result of the pipes being cut to size, and previously ended up in the incinerator.
This material is now transported multiple times a year to Geberit. Project Manager Silvio Gächter says: “The incoming goods inspection is the most important step. We have to ensure that the material is clean and sorted.”
A win-win situation
“Currently, we can add up to one-fifth reused material during production,” explains Silvio Gächter. This reuse is not only environmentally sound, but also economical: “Processing scraps is cheaper than buying new material, and the prefabrication companies also save on waste disposal costs.”