Digital bloodhound
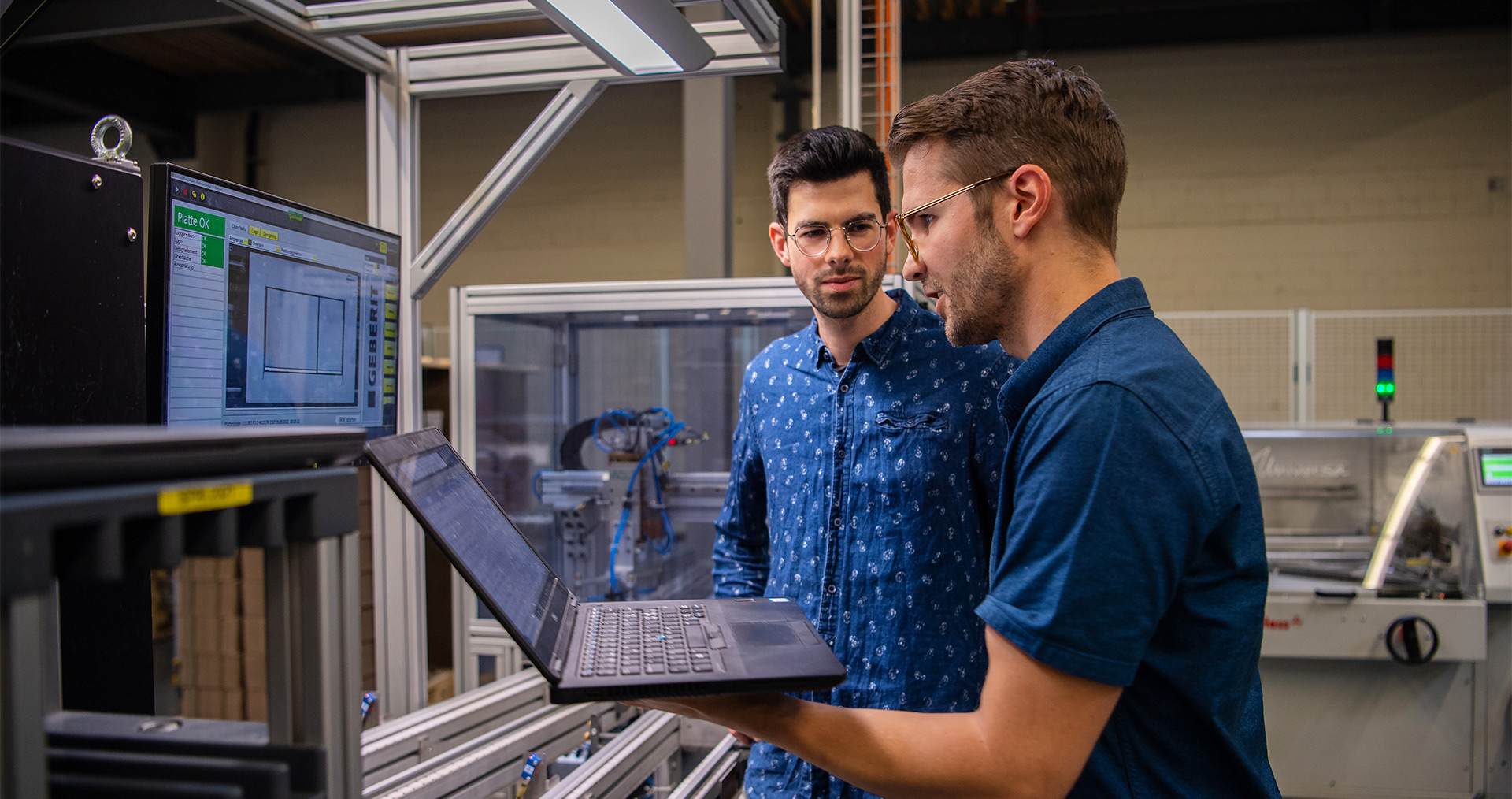
Nothing escapes the camera. Its task is to find the smallest defects and flaws in the freshly produced actuator plates. Thanks to a new piece of software, improved evaluation of the collected data is now possible.
The freshly moulded and assembled actuator plates roll down the conveyor belt at the Geberit plant in Rapperswil-Jona (CH). Shortly before the packaging line, they enter a black box. While they come out exactly as they went in, this process is not without consequences. The box contains cameras that analyse the condition of the products under ideal lighting conditions and find faults.
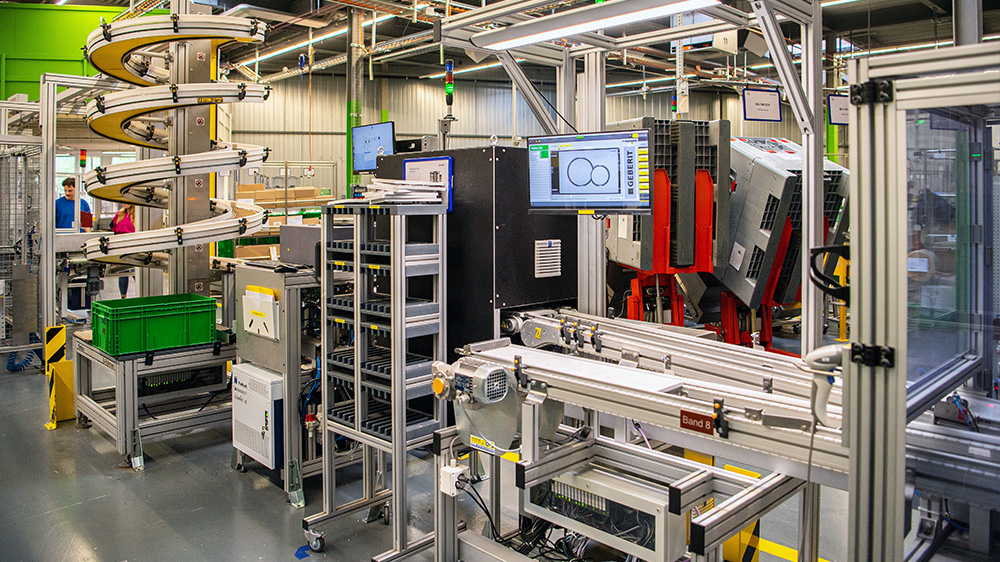
Significantly more powerful
This has been the status quo for many years. The QualiVision systems have been installed at the plant in Rapperswil-Jona since 2008. However, they have now suddenly become much more potent. Together with his team, doctoral student Arne Seeliger has developed software that evaluates the mountain of data from the cameras. As a result, the system determines where the cause of a problem is. According to Arne Seeliger, this has two advantages – one short-term and one long-term. The short-term advantage is as follows: “We can program the software to sound an alarm when a threshold value is exceeded and a product is rejected.” Those responsible can then quickly identify and remedy the source of the error.

Economical optimisation
The long-term benefits of the new software will continue to increase. According to Christian Landolt, project manager for quality assurance, this involves the evaluation of the data pool over longer periods of time. “We can then find out which errors occur most frequently.” He explains that numerous process optimisations have already been implemented. This is also reflected economically. “Thanks to improved data evaluation, we can achieve significant annual savings,” comments Arne Seeliger.