Aus 17 wird 1
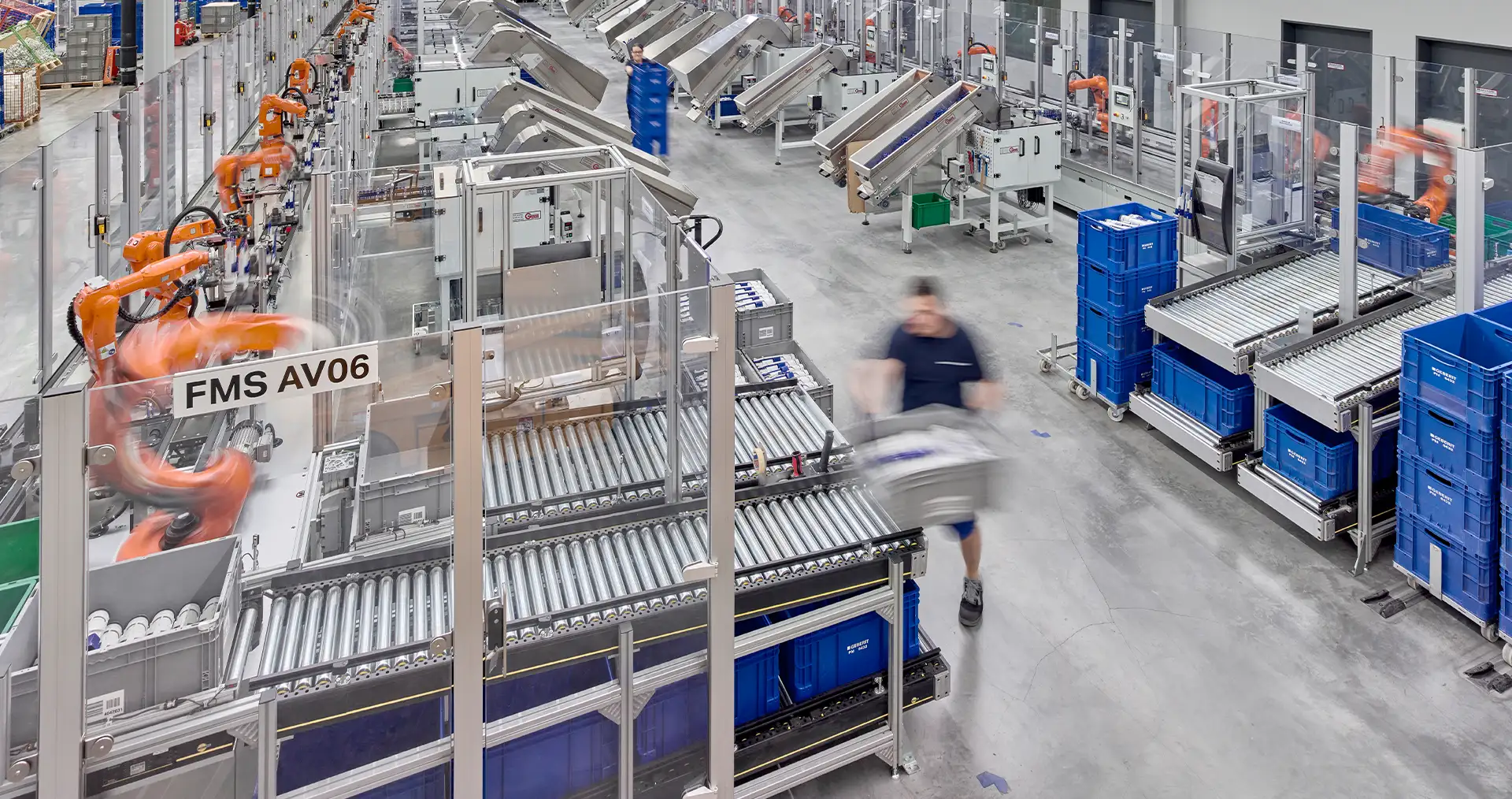
Sie heissen Linda, Marie oder Ramona – benannt nach deutschen und Schweizer Fussballspielerinnen. Gemeint sind die 30 Roboterarme des Montagesystems zur Herstellung des Spülventils Typ 212 in Pfullendorf (DE).
Die Verantwortung für die hochpräzise Eigenkonstruktion liegt seit dem Projektstart bei Fabian Hiller, Projektingenieur in Pfullendorf. Unter seiner Regie entsteht das flexible Montagesystem termin- und kostengerecht innerhalb von anderthalb Jahren – konstruiert und aufgebaut vom werkseigenen Team, bestehend aus Konstrukteuren, Steuerungstechnikern und Informatikern. Lediglich spezifische Komponenten wie die orangefarbenen Roboterarme stammen von externen Lieferanten. «Ziel ist es, die Produktionszeit des Spülventils zu optimieren, die Komplexität zu reduzieren und damit die Mitarbeitenden zu entlasten», resümiert Fabian Hiller.
17
Einzelteile
Aus 17 Einzelteilen setzt sich ein Spülventil Typ 212 zusammen.
Maximale Flexibilität
Laufen die beiden Linien auf Hochtouren, können pro Tag mehrere Tausend Spülventile hergestellt werden. Dafür sind drei Mitarbeitende notwendig. Sie bedienen die Anlage, befüllen sie mit den 17 verschiedenen Einzelteilen und entnehmen die fertigen Spülventile. Es ist aber auch möglich, das flexible Montagesystem mit nur einer Person zu betreiben. Dann liegt der Output entsprechend tiefer. So kann auch das Personal innerhalb der Produktionshalle besser zwischen den verschiedenen Anlagen eingeteilt werden. «Diese Flexibilität ist eine der grössten Stärken der neuen Produktionslinien», hält Fabian Hiller fest. Praktisch ist auch die modulare Bauweise: Durch das Einschieben zusätzlicher Module können nachträglich neue Bearbeitungsstationen integriert werden – die Anlagen sind also bestens auf künftige Innovationsschritte vorbereitet.